Mastering Precise Molding in Metal Fabrication
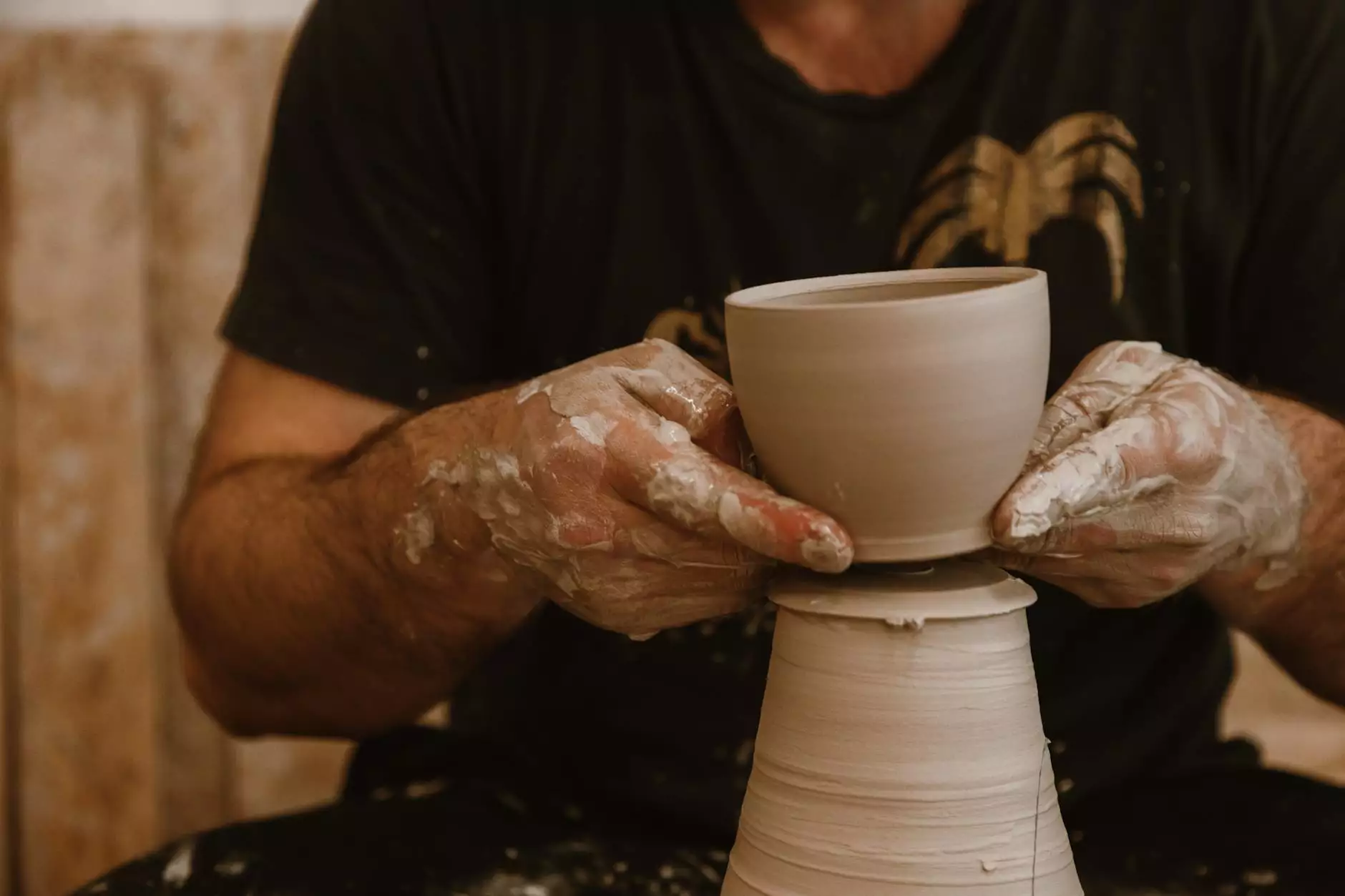
In the competitive landscape of metal fabrication, achieving excellence is not just about utilizing advanced machinery; it is about the art of precise molding. This intricate process sits at the core of high-quality metal works, where the fusion of innovation and craftsmanship defines the standard of production. At Deep Mould, we pride ourselves on our relentless pursuit of precision, ensuring that every piece we fabricate meets the highest industry standards.
The Importance of Precise Molding in Metal Fabrication
Understanding the significance of precise molding in metal fabrication is crucial for producing components that not only meet but exceed client expectations. The precision involved in molding affects various aspects of production, including:
- Product Quality: Higher precision means lower tolerances and better-fitting parts.
- Cost Efficiency: Reducing waste and minimizing the need for rework can drastically lower production costs.
- Speed of Production: Precise molds lead to faster production times, allowing companies to meet tight deadlines.
- Design Flexibility: Precise molding allows for complex designs that enhance product functionality.
What Is Precise Molding?
Precise molding refers to the technique of forming materials into specific shapes with exacting dimensions and tolerances. This process is crucial in industries where interoperability and functionality are paramount. The molding process can utilize different materials, with metal being one of the most commonly used due to its durability and versatility.
Key Techniques in Precise Molding
The following techniques play an essential role in achieving precise molding in metal fabrication:
1. Die Casting
Die casting involves forcing molten metal into a mold cavity under high pressure. This technique is widely used for its ability to produce highly intricate designs with excellent surface finish and dimensional accuracy.
2. Injection Molding
Although primarily associated with plastics, injection molding can also apply to metals through the use of specialized materials. This method is known for producing parts with a consistent shape and size.
3. 3D Printing
With advancements in technology, 3D printing has emerged as a groundbreaking method for creating molds. Metal 3D printing allows for rapid prototyping and manufacturing of parts that were once considered impossible due to design constraints.
4. CNC Machining
Computer Numerical Control (CNC) machining is a subtractive method where materials are precisely cut to design specifications. CNC machining ensures a high degree of accuracy and repeatability, essential for precise molding.
Challenges in Achieving Precise Molding
While the advantages of precise molding are clear, the path to achieving it is laden with challenges. Key issues include:
- Material Variability: Different metals have different properties, affecting how they respond during the molding process.
- Temperature Control: Precise temperature regulation is essential to avoid defects in molded parts.
- Tool Wear: Over time, molds and dies experience wear that can affect precision, necessitating regular maintenance and replacement.
- Complex Geometries: Intricate designs can pose significant challenges in achieving accurate molds without compromising material integrity or functionality.
How Deep Mould Ensures Precision in Molding
At Deep Mould, we leverage a combination of state-of-the-art technology, highly skilled personnel, and comprehensive quality control measures to ensure that we provide our clients with unmatched precision in metal fabrication.
Investing in Technology
We continually invest in the latest machinery and software that enhances our molding processes. By utilizing high-performance CNC machines, advanced die casting technologies, and sophisticated design software, we optimize every aspect of production.
Expertise and Training
Our team consists of seasoned professionals who undergo regular training to stay abreast of the latest developments in metal fabrication technology. This comprehensive understanding of the processes allows us to mitigate risks and enhance precision consistently.
Quality Control Protocols
We implement stringent quality control measures at every production stage. From initial design testing to final inspections, we ensure that every unit produced adheres to the highest standards. Our commitment to quality guarantees that our clients receive only the best products.
The Future of Precise Molding in Metal Fabrication
The evolution of technologies such as artificial intelligence and machine learning is poised to revolutionize the precise molding industry. As these technologies become integrated into manufacturing processes, they will enhance predictive maintenance, further minimize human error, and optimize workflows.
Embracing Sustainability
Future advancements in molding will also focus heavily on sustainability. The implementation of materials that are not only precise but also environmentally friendly is becoming a priority. Deep Mould is committed to adopting practices that reduce environmental impact while maintaining quality.
Conclusion: The Deep Mould Commitment to Precise Molding
In conclusion, precise molding is a cornerstone of any successful metal fabrication process. At Deep Mould, we are dedicated to advancing our methods and practices to provide precision that our clients can rely on. Our focus on quality, innovation, and efficiency positions us as a leader in the field, guaranteeing that each project meets the highest standards of excellence.
As we look to the future, we remain committed to enriching the metal fabrication landscape through continued innovation and a steadfast dedication to precision. For inquiries or to learn more about our offerings, feel free to visit our website or reach out to our expert team.