Understanding Injection Molding of Plastics: A Comprehensive Guide
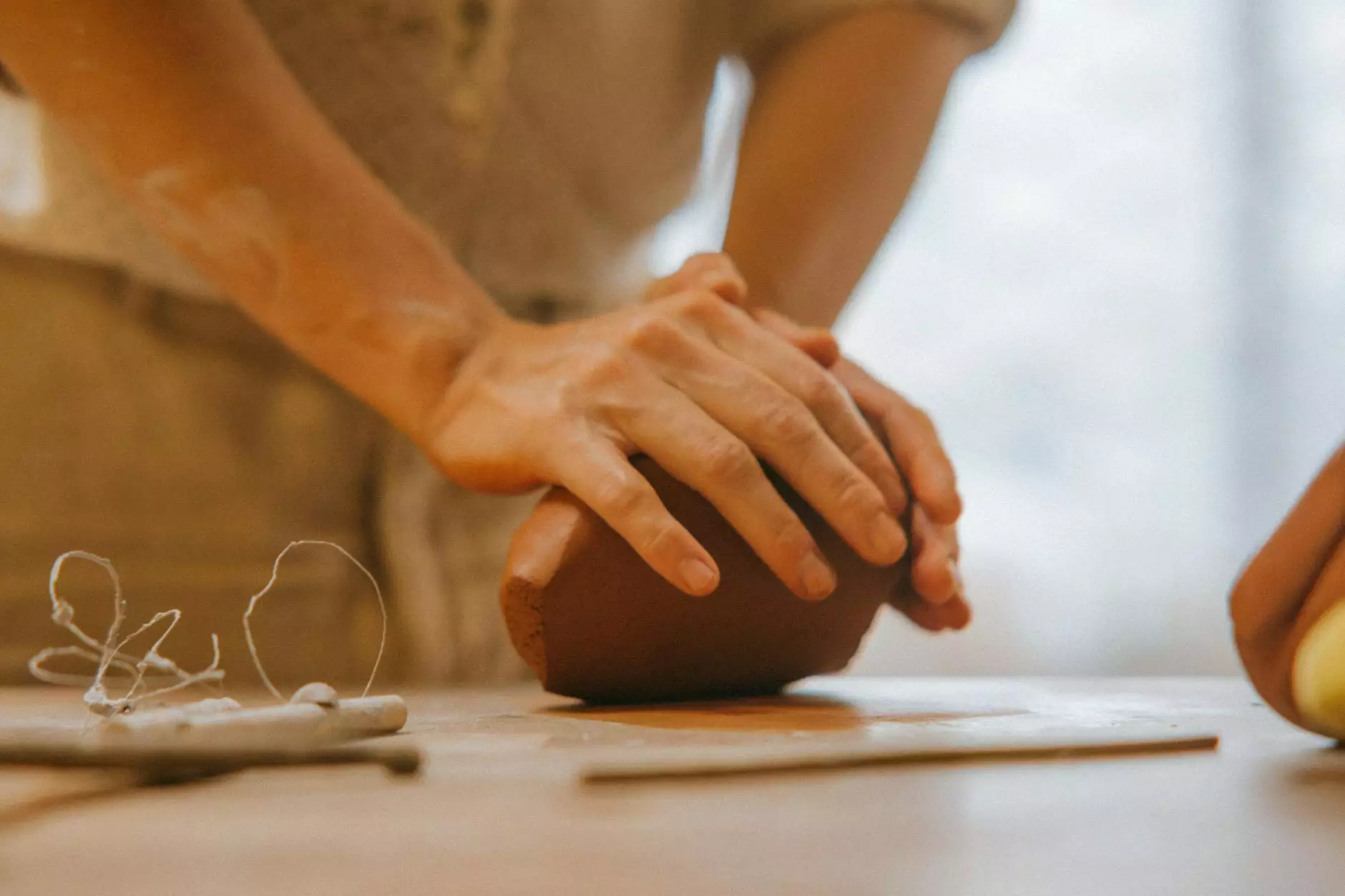
Injection molding of plastics is an essential manufacturing process that plays a pivotal role in various industries, particularly in the realms of electronics and medical supplies. This process involves the creation of parts by injecting molten plastic into a mold, allowing for precision, efficiency, and scalability in production. In this article, we will delve deep into the techniques, applications, and benefits of injection molding, particularly emphasizing its implications for Nolato—a leader in providing solutions for various industries.
The Basics of Injection Molding
At its core, injection molding is a systematic process that transforms raw plastic into engineered components. The basic steps involved in injection molding of plastics are as follows:
- Material Selection: The process begins with choosing the right type of plastic resin suitable for the desired properties and functions of the end product.
- Melting the Material: The selected plastic is heated until it reaches a molten state, allowing it to flow easily into a mold.
- Injection: The molten plastic is injected into a precisely designed mold under high pressure.
- Cooling: Once the mold is filled, the plastic is cooled to solidify the shape.
- Demolding: After sufficient cooling, the mold is opened, and the finished part is ejected.
- Finishing Touches: Additional processes may include trimming, surface finishing, or assembly of parts.
Applications of Injection Molding in Electronics
The electronics industry is one of the most significant beneficiaries of the injection molding process due to the need for high-precision components. Here are some applications:
1. Enclosures and Housings
Injection molding is widely used to manufacture enclosures for various electronic devices. These housings need to be durable, lightweight, and able to protect the internal components from environmental hazards. The flexibility in designing complex geometries allows manufacturers to create intricate designs that align with brand aesthetics while ensuring functionality.
2. Connectors and Switches
Connectors and switches are essential components in any electronic device. The injection molding process enables mass production of these tiny parts with exact specifications to ensure reliability and performance.
3. Insulation Parts
Electrical insulation is a critical aspect of electronics. Injection molding allows for the creation of insulating parts that conform to specific safety standards, ensuring that devices function efficiently without the risk of electrical hazards.
Significance of Injection Molding in Medical Supplies
The medical equipment sector has stringent requirements for quality and precision. Injection molding of plastics serves an essential purpose within this industry. Here’s how:
1. Custom Medical Devices
Customization is vital in medical devices, and injection molding enables the production of tailored components that meet specific clinical needs. From surgical tools to diagnostic equipment, the precision of molded parts is paramount.
2. Sterilizable Components
Medical supplies often require sterilization to ensure patient safety. Injection molded plastics can be engineered to withstand sterilization processes without degrading, ensuring durability and reliability in critical applications.
3. Cost-Efficiency
In the medical field, cost-efficiency in manufacturing can lead to lower healthcare costs overall. The scalability of injection molding allows for the mass production of medical supplies, thereby reducing prices for consumers and healthcare providers alike.
Advantages of Injection Molding
There are several key advantages that make injection molding of plastics a preferred manufacturing method:
- High Production Rates: Once the initial mold is created, injection molding can produce thousands of identical parts quickly, making it ideal for large production runs.
- Precision and Consistency: Injection molding produces parts with high dimensional accuracy and repeatability, essential for electronics and medical applications.
- Material Efficiency: Minimal waste is generated during the process, and excess material can often be recycled, making it an environmentally friendly option.
- Versatility: A wide range of plastic materials can be used, allowing for the production of various components tailored to specific applications.
- Complex Geometries: Injection molding allows for the design of intricate shapes that are often difficult or impossible to achieve through other methods.
The Future of Injection Molding
As technology continues to evolve, so does the field of injection molding of plastics. Here are some trends and innovations shaping the future:
1. Advanced Materials
New materials, including bio-based and recyclable plastics, are gaining traction in the injection molding process. These materials not only cater to environmental sustainability but also enhance product performance.
2. Automation and Smart Manufacturing
Automation and the integration of smart technologies are transforming traditional manufacturing processes. By employing robotics and IoT (Internet of Things) in injection molding, manufacturers can achieve higher efficiency, better quality control, and reduced operational costs.
3. Customization and On-Demand Manufacturing
The rise of 3D printing technology is influencing injection molding, offering unprecedented levels of customization and the potential for on-demand production, which can drastically reduce lead times and inventory costs.
Conclusion
In summary, injection molding of plastics is a critical manufacturing technique that significantly impacts the electronics and medical supply industries. Its advantages, ranging from high precision to cost efficiency, make it an essential part of modern production methodologies. As companies like Nolato continue to innovate and adapt to industry needs, the future of injection molding looks promising, full of opportunities for enhancing product quality and manufacturing processes.
References and Further Readings
For those looking to dive deeper into injection molding of plastics and its applications in various industries, the following resources may be beneficial:
- Nolato's Official Website
- Plastics Engineering Magazine
- Technical Pursuit for Injection Molding Insights
This comprehensive guide serves as a valuable resource for understanding the vital role that injection molding of plastics plays in shaping the future of manufacturing across critical sectors.