Understanding the Role of Plastic Mold Makers in Modern Manufacturing
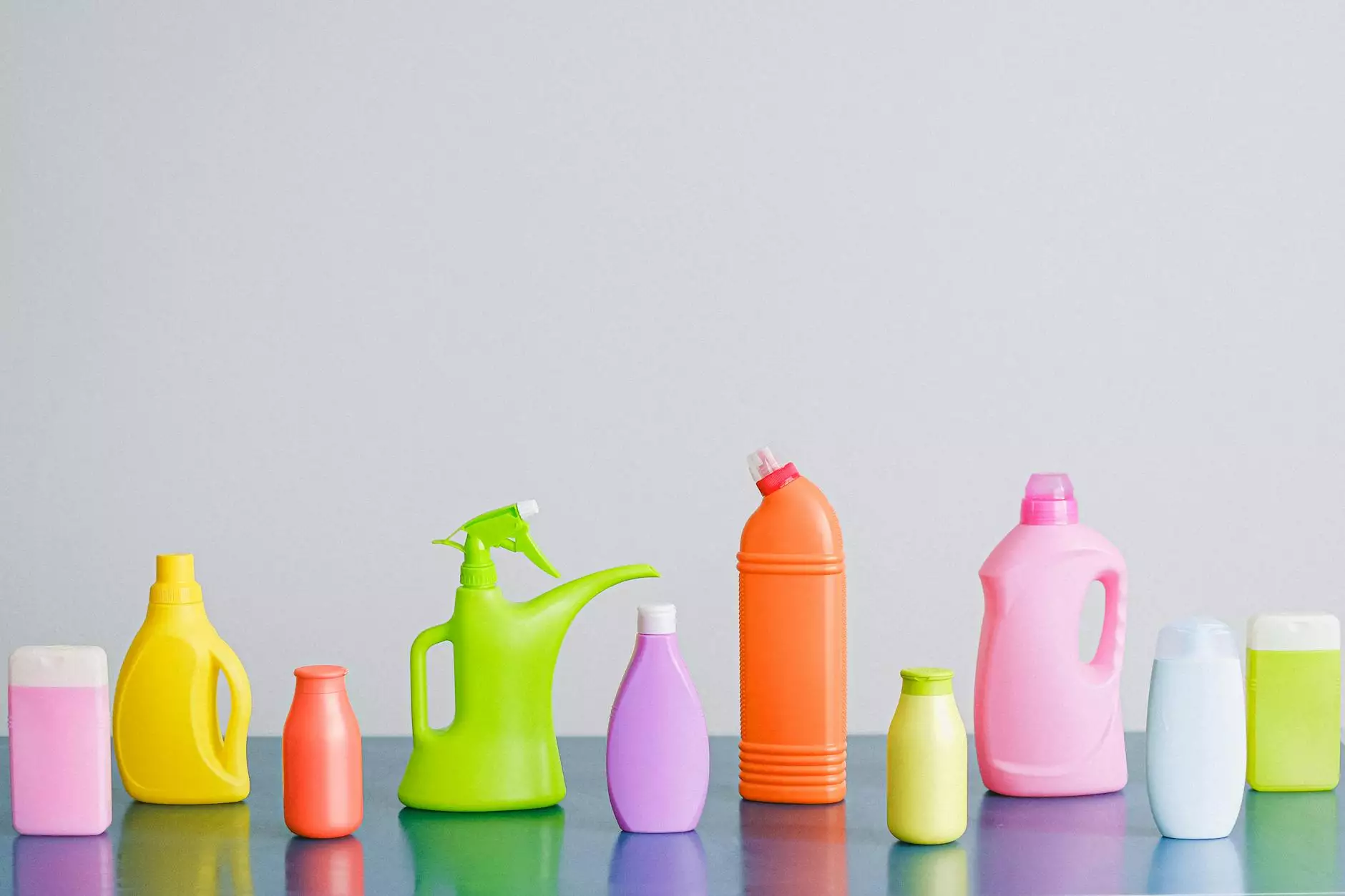
In the ever-evolving landscape of modern manufacturing, the significance of plastic mold makers cannot be overstated. These professionals play a pivotal role in transforming ideas into tangible products, enabling industries to thrive in a competitive market. This article delves deep into the world of plastic mold makers, detailing their processes, the technologies they use, and the substantial impact they have on various sectors.
The Importance of Plastic Molds in Manufacturing
Plastic injection molding is a highly efficient manufacturing process that allows for the mass production of plastic parts. The quality of the plastic molds directly affects the overall quality of the final products. Below are some critical reasons why plastic molds are indispensable in modern manufacturing:
- Cost Efficiency: High-quality plastic molds can significantly reduce production costs by increasing the speed and efficiency of manufacturing.
- Design Flexibility: Molds can be designed to create complex shapes and structures, allowing for innovative product designs that meet market demand.
- Consistency: Molding processes produce consistent results, ensuring that every piece manufactured meets predefined specifications and quality standards.
- Material Versatility: Plastic molds can be used with various materials, providing manufacturers with the flexibility to choose the best fitting for their needs.
What Do Plastic Mold Makers Do?
Plastic mold makers are skilled professionals who specialize in designing, creating, and maintaining molds used in the injection molding process. Their work encompasses several stages, each crucial to ensuring that the final products meet the required standards. Here’s a breakdown of their significant responsibilities:
1. Design and Engineering
The first step in mold-making involves designing the mold based on the specifications provided by the client. Here, precision is key. The mold design must align with the end product’s functional and aesthetic requirements. Advanced computer-aided design (CAD) software is often employed to visualize and refine mold designs before production.
2. Manufacturing the Mold
After the design is approved, mold makers proceed to manufacture the molds. This involves:
- Machining: Using CNC (Computer Numerical Control) machines, mold makers precisely shape and form the mold components.
- Fabrication: Skilled technicians hand-assemble smaller mold parts to ensure they fit seamlessly.
- Testing: Initial tests are conducted to ensure the mold functions correctly and produces parts that conform to specifications.
3. Maintenance and Repair
Mold maintenance is vital for sustaining production quality. Regular checks and repairs are necessary to prevent mold degradation, which could lead to costly downtime. Mold makers are responsible for implementing maintenance schedules that prolong the life of the molds and enhance productivity.
The Technologies Behind Plastic Mold Making
In recent years, advancements in technology have significantly transformed the mold-making process. Here are a few technologies that plastic mold makers commonly utilize:
1. CAD and CAM Software
Computer-Aided Design (CAD) and Computer-Aided Manufacturing (CAM) software streamline both the design and manufacturing processes. These tools assist in creating precise designs and controlling machining operations, allowing for greater accuracy and efficiency.
2. 3D Printing
3D printing has emerged as a revolutionary technology in mold making, enabling rapid prototyping. Mold makers can create test molds quickly, allowing for immediate feedback and adjustments before final production.
3. Injection Molding Machines
Modern injection molding machines are equipped with advanced features that enhance production speed and quality. Features such as improved temperature control, automation, and real-time monitoring systems ensure optimal performance and reduced waste.
Choosing the Right Plastic Injection Mould Manufacturer
Selecting an appropriate plastic injection mould manufacturer is instrumental for businesses that rely on plastic components. Here are several factors to consider when choosing a manufacturer:
1. Experience and Expertise
Look for a manufacturer with a proven track record in the industry. An experienced company will have the technical know-how and problem-solving abilities to handle various challenges.
2. Quality Assurance Processes
Ensure the manufacturer has established quality control systems to guarantee the precision and consistency of their molds. Certifications such as ISO 9001 can indicate a commitment to high manufacturing standards.
3. Customization Options
The ability to customize molds to specific requirements is crucial. A good manufacturer will work with you to create tailored solutions that fit your needs.
4. Communication and Support
Effective communication is key throughout the mold design and production process. Choose a manufacturer that prioritizes customer service and transparent communication.
Future Trends in Plastic Mold Making
The field of plastic mold making is continuously evolving, with several trends shaping its future:
1. Integration of Artificial Intelligence (AI)
AI is beginning to play a role in optimizing mold designs and predictive maintenance. By analyzing data from previous projects, AI systems can offer suggestions for improvements and anticipate issues before they arise.
2. Sustainable Practices
With increasing environmental concerns, many manufacturers are seeking eco-friendly materials and processes. Mold makers are expected to adopt more sustainable practices, such as using recycled materials and reducing energy consumption.
3. Increased Automation
Automation of mold-making processes can enhance efficiency and reduce the potential for human error. Automated systems can operate at high speeds, ensuring faster turnaround times for clients.
Conclusion
In conclusion, plastic mold makers are integral to the manufacturing process, providing essential services that drive innovation and efficiency in numerous industries. By understanding their role, the technologies they utilize, and the importance of choosing the right manufacturer, businesses can better position themselves for success in today’s competitive landscape.
As the industry continues to evolve, staying informed about trends and advancements will empower manufacturers to make strategic decisions that lead to sustainable growth and enhanced product offerings.